Frýdecko-místecký startup 24 Vision Systems vyvíjí řešení kontroly kvality na bázi umělé inteligence. Jeho neuronové sítě a kamery už využívá například automobilka Hyundai a pilotně je testuje také Škodovka. Umělá inteligence údajně dosahuje takřka stoprocentní úspěšnosti a překonává i lidské kontrolory. Firmě také pomohl úspěch v soutěži CzechInvest Startup Challenge, ve které nedávno obsadila první místo.
V letošním roce firma dostala seed investici od skupiny M.L. Moran a v příštím roce se chystá expandovat do Německa a Španělska. Navzdory komplikované situaci, kdy koronavirus tvrdě dopadl na evropské automobilky, se frýdecko-místecký startup nedostatku zájmu nebojí. Jak říká spoluzakladatel a CTO 24 Vision Systems Martin Cviček, firmy prý do automatizace investují i navzdory tomu, že obecně musí šetřit.
K čemu je váš systém dobrý? Co všechno umí?
Je to stanoviště kontroly kvality založené na AI. Hodnotí, jestli je výrobek bez defektu a zároveň konfiguračně správný. „Bez defektu“ znamená, že když řešíme třeba dveře od auta, tak na jejich vnitřní straně je různé množství vzorů a vybavení. A my hledáme, jestli tam není nějaká díra, špína, škrábanec, nebo třeba zlomenina v konstrukci. Co se pak týče konfigurační správnosti, tam zase sledujeme, zda výrobek odpovídá požadavkům zákazníka.
V automobilkách, konkrétně třeba ve Škodovce, řešíme pilotní projekt pro kontrolu dveří, kdy na nich kontrolujeme konfigurační správnosti, jestli mají stejnou výplň, zda je na nich správná konfigurace tlačítek, jestli mají správný steh, a tedy jestli se všechny dveře skutečně shodují. Dříve toto všechno museli dělat lidé. Pro srovnání, jejich úspěšnost se při kontrole pohybuje mezi 60 a 80 %, náš systém to zvládá na 99 %.
Používáte příklad z automobilky. Je váš systém vhodný jen pro tento typ průmyslu, nebo se dá použít v podstatě kdekoliv?
Dá se použít kdekoliv. S automobilkami jsme začali proto, že seděly do našeho portfolia. Náš systém je jedinečný hlavně v tom, že umí zkontrolovat zmíněnou konfigurační správnost. To znamená, že má napojení do MESu (Manufacturing Execution System, výrobní informační systém), je schopen sám zjistit, co má kontrolovat, a potom to udělá. A zároveň umí prohlédnout hodně oblastí najednou. Nekontrolujeme tedy jen škrábanec, ale na každé sedačce třeba sto různých věcí tak, aby byla celá sedačka v dobré kvalitě.
Proč se takové funkce hodí zrovna do automobilek?
Máte tam rychlou frekvenci linky a zároveň potřebujete zajistit vysokou kvalitu, protože za její nedodržení hrozí velká penalizace. Jsme startup, nejsme schopní hned pokrýt všechno. V letošním roce jsme cílili jen na automobilový sektor v České a Slovenské republice, abychom si tu udělali nějaké jméno, a pak chceme jít do Evropy. V ostatních oblastech máme nějaké pilotní projekty, které přišly spíše ze strany zákazníků, kteří nás kontaktovali sami. Hlavně jde o oblasti spotřebního zboží a elektroniky, pak také potravinářství nebo zemědělství.
Vaše technologie zní dost sofistikovaně. Jak ten nápad vůbec vznikl?
Jsme startup, který vznikl z mateřské firmy TinT. Ta je na trhu 25 let a řeší IT pro lokální zákazníky ze severní Moravy a pro Hyundai. Před pěti nebo šesti lety se na nás z Hyundai obrátili s otázkou, jestli jsme schopní poskytnout na míru stavěné řešení pro kontrolu kvality. My řekli, že ano, a dva roky jsme to vyvíjeli. Řešení nakonec sklidilo úspěch a domluvili jsme se, že to zkusíme produktizovat. Z toho po roce a půl vznikl 24 Vision Systems.
To jsou tedy začátky s jedním řešením. Jak dlouho zatím trval vývoj celé technologie?
Asi pět let. První rok dva trvá pochopit potřebu trhu a zákazníka, co vlastně hledá. Zákazník vám hned zkraje nevyspecifikuje přesné požadavky, co potřebuje, na to s ním musíte po nějakém brainstormingu přijít. A druhá, asi nejdelší, fáze byla najít to vhodné řešení. My jsme hned začali se sofistikovanou technologií využívající neuronové sítě a deep learning. Ale i v rámci neuronek máte dnes možná tisíce různých druhů sítí, takže byl nutný dost velký průzkum, abychom našli správné kombinace a vybrali jsme to řešení, které je dostatečně univerzální, ale na druhou stranu dostatečně přesné a splňovalo parametry automotive.
A když se zamyslíte nad procesem vývoje a nad tím, co jste vše museli překonat, tak co z toho bylo nejtěžší?
Není to můj první startup, už jsem se podílel na více projektech, a pro mě je vždycky nejdůležitější a zároveň nejtěžší milovat své zákazníky (smích). A to znamená vůbec mít zákazníky. Je to ten nejtěžší úkol, ale na druhou stranu ten nejdůležitější. Jedině zákazník je schopný validovat řešení a posunout vás dále. A co se týká samotného vývoje, tam nám nejvíce času zabral research a výběr správné architektury neuronové sítě. Dnes už to funguje tak, že máme nějaké základní portfolio neuronových sítí, které nakonfigurujeme ve vhodné kombinaci na daný problém. Toto portfolio postupně rozšiřujeme o další dle nových požadavků trhu.
Už několikrát padlo slovo neuronová síť. Pojďme se na to trochu víc zaměřit. Jak je ve vašem systému přesně využíváte?
Uvedu to zase na příkladu. Vision systémy jako takové jsou na trhu nejméně 20–30 let. Fungují tak, že jako předlohu máte nějaký obrázek, pak si uděláte aktuální snímek, a když ty dva obrázky dáte na sebe, sledujete, nakolik si odpovídají, a sledujete shodu s předlohou. Takové systémy pořád zaujímají 90 % místa na trhu vision systémů. Nevýhodou ale je, že jsou hodně přesné, takže tu fotku, kterou pořizujete, musíte mít v přesně stejné pozici, jako je předloha, včetně světelných podmínek.
Když si vezmu neuronovou síť, tak tam nemáte jednu předlohu, ale máte jich třeba 10 000, a to v různých situacích a světelných podmínkách. Neuronovou síť naučíte reálné prostředí, ona vezme v potaz všechny kombinace a ty porovnává s aktuálním snímkem. Neuronová síť je proto daleko více rezistentní vůči vlivům, ke kterým dochází, ale na druhou stranu si uchovává přesnost, protože pracuje na podobném principu jako člověk. Bere v potaz vzájemné závislosti. Neporovnává jenom jeden pixel, ale větší komplex obrázku ve strašně velkém množství kombinací.
Nemůže se ale stát, že když má váš systém zkontrolovat dveře nebo sedadlo a na výrobku je nějaká chyba, škrábanec, šmouha, tak si to neuronka naopak splete se špatným odrazem světla a podobně?
Škrábanec je dobrý příklad, to jsme zrovna řešili minulý měsíc. Určitě se to může stát, ale je to mnohonásobně méně pravděpodobné než u klasického visionu. Neuronka se to dokáže naučit rozpoznávat, a to lépe než člověk, protože jde do mnohem většího detailu. Když se na to dívá člověk, tak mu to připadá stejné. Ale neuronka najde závislosti a rozezná odraz světla od škrábance. Samozřejmě se ale může stát, že se síť splete, a proto když nasazujeme náš systém, následuje tuning period, zlepšovací období, kdy operátor, který je na té lince ještě nějakou dobu (týden, dva nebo měsíc), má možnost jí dát zpětnou vazbu, že ten systém vyhodnotil něco špatně. A tím se systém ještě doučuje. Problém je, že neuronky potřebují k tréninku dostatečné množství vstupních obrázků.
Jak to učení v případě vašeho systému vypadá? Necháváte kamery nějakou dobu zaznamenávat dění na lince a pak ručně označujete chyby?
Je tam několik procesů, toto je jeden z nich a asi nejčastější. Většinou to funguje tak, že když přijdete do fabriky, koncovou kontrolu dělá člověk. Takhle to funguje na drtivé většině českého trhu a ještě jsme se nesetkali s tím, že by někdo měl hotové řešení právě na oblast koncové komplexní kontroly kvality. A ten člověk má na základě dřívějších zkušeností vytvořený seznam věcí, které kontroluje. To je pro nás vstupní informace. Některé věci z toho seznamu ani nemusíme trénovat přes ruční označování. Jenom pořídíme pár obrázků a řekneme jí „ten obrázek je celý dobře, ten obrázek je celý špatně“. To je takzvaný přístup unsupervised, bez učitele, kdy je neuronka schopná sama najít chybu na obrázku a tu pak detekovat.
Nevýhodou takového přístupu je ale citlivost na externí vlivy, je to tak?
Ano, proto se většinou používá přístup s učitelem, tedy tak, jak jste zmiňoval, že musíte té síti skutečně říkat, jestli je ta věc na obrázku nějaká chyba, nebo je to nějaká komponenta, kterou má porovnávat. A to musíte udělat na několika, ideálně třeba padesáti obrázcích. Ty obrázky se pořizují různým způsobem. Nejlehčí a nejčastější je skutečně to, že se v produkci na kontrolní stanoviště nainstaluje pár kamer, které skutečně jeden, dva, tři dny, někdy i týden, sbírají obrázky a ty se potom používají na učení. V jiných případech, pokud se ty výrobky dají vzít ven, to děláme v naší laboratoři. Máme vlastní linku, na které testujeme a učíme menší produkty.
Co se týče samotné práce neuronových sítí, jaké různé procesy se tam uplatňují?
Neuronky mají pár základních typologií, tedy detekční, klasifikační a segmentační. U detekční většinou označíte síti nějaký předmět, který má hledat. Označíte třeba kočku a ona hledá kočku. Segmentační potom je, že jsem schopen v rámci toho obrázku vytvořit takzvaný polygon nebo štětcem vymalovat konkrétní plošku různého tvaru a ona mi pak na úrovni pixelů hledá podobný objekt i na tom reálném obrázku. To se používá, když na velkém snímku hledáte nějaký malý specifický detail. A ta třetí klasifikační funkce znamená, že neuronka vstupní informaci klasifikuje do několika tříd. Třeba v případě, že budu mít 20 etiket, tak si udělám 20 klasifikačních tříd. Ona mi ty etikety krásně rozklasifikuje a já už si je potom jsem schopen vyhodnotit a zkontrolovat, jestli je v procesu někdo nezaměnil. Tyto tři základní typy neuronek se pak rozšiřují o další prvky typu detekce struktury, barev apod. A celý náš systém běží na bázi něčeho, čemu říkáme problémy. Máme třeba 20 nebo 30 problémů představujících typické věci, které uživatel potřebuje zkontrolovat. Ty si různě nakombinujete a jste schopen pokrýt kontrolu kvality téměř jakéhokoliv produktu.
Když si ten systém představím v praxi, tak jak to v té továrně vypadá? Je tam nějaký rám s kamerami?
Přesně tak, za prvé je tam rám s kamerami. Kromě kamer ale postupně pronikáme i do ostatních zařízení. Spolupracujeme s firmou Advacam, což je dodavatel rentgenů. Je to také hodně sofistikovaný startup a řekl bych, že mají nejpřesnější a nejhlubší rentgeny v celé branži na světě. Díky nim jsme schopní jít „dovnitř“ těch produktů a zkontrolovat vnitřní strukturu. Oni třeba používají rentgeny na kontrolu letadel při výrobě křídel, zda je tam správný materiál se správnou strukturou a jestli tam náhodou někdo nezapomněl šroubovák. A kromě rentgenů využíváme také infrakamery a termokamery. Termální kamera třeba umožňuje zkontrolovat vyhřívací kabel v sedačce. A to nejen z hlediska toho, zda není kabel přerušený, ale i jestli má správný tvar pro vyhřívání celé sedačky. Samotné stanoviště pak obsahuje určitý počet kamer, které skenují výrobek z těch stran, ze kterých chceme detekovat problém.
A jak probíhá vyhodnocování těchto informací?
Kamery jsou připojené na server nebo pracovní stanici, která provádí analýzu obrázků. Neuronka tam nevyužívá CPU, ale kvůli vyššímu výkonu vše počítá grafická karta. V podstatě je ten hardware podobný herním počítačům. Neuronka pak vyhodnotí záznam a analytický software řekne, jestli je výrobek v pořádku. My jsme pak v reálném čase schopní říct výrobní lince „tento výrobek je špatný, dej ho na boční kolej“, nebo „ten je dobrý, můžeš pokračovat“. Případně výsledky posíláme do nějakého nadřazeného systému, kde informace v reálném čase poskytujeme pracovníkům výroby. Důležitá je ale business inteligence nástavba, kde už zákazník může provádět lean analýzu a analytiku toho, kde je ve výrobě nějaké úzké hrdlo, na které se mají zaměřit.
A pokud systém detekuje vadný kus, musí ho linka pokaždé vyřadit?
Vždy, když systém detekuje vadný díl, označíme úroveň vady. Pokud je to v toleranci, označíme problém kvůli záznamu, ale díl pokračuje dál. Potom jsou to vadné díly, které se dají hned opravit, ty jedou na boční kolej k opravě. A nakonec máme vadné díly na vyřazení. Většinou u zjištěných defektů stačí oprava přímo na místě v taktu linky. Když si představíte sedačky nebo dveře, tak pokud v tom taktu výrobní linky nestihnete poškozené sedačky nebo dveře opravit, celé auto se posouvá dál, takže je maximální snaha opravit výrobek v taktu linky, kdy je třeba pětiminutový buffer, aby nemuseli rušit objednávku celého auta a znovu ho dávat do výroby. Čekají tam operátoři, kteří většinu vad opraví. Ale pokud je to skutečně velké poškození nebo díl potřebuje takovou opravu, že nejde udělat na místě, výrobek jde na vyřazení. U dveří se třeba vyřazují všechny dveře konkrétního auta a čeká se, až budou hotové nové.
Na jakých přesně technologiích ta stanoviště běží?
Snažíme se naše řešení stavět co nejuniverzálněji a dokážeme integrovat i třeba neuronové sítě třetích stran. Na trhu je několik firem, včetně velkých hráčů, například Cognex, se kterými se bavíme o spolupráci. Chceme být spíš platformou, která shora zajišťuje integraci, a pokud je na nějaký produkt nebo problém vhodná neuronka třeba od Cognexu nebo dalších firem, tak ji integrujeme, abychom pokryli konkrétní požadavek od zákazníka. Když se bavíme o kamerách, zase můžeme integrovat různé typy výrobců Basler, Sick, Cognex, Axis a tak dále. Máme nadefinované rozhraní pro různé typy kamer. To samé platí i o rentgenech nebo infra a termálních kamerách. Dále používáme hardware od HP nebo Siemens. Celá logická vrstva naší aplikace je univerzální, stavíme to jako cloud native, takže nezáleží, na čem aplikace běží, a jsme schopní náš systém škálovat na různé platformy.
Váš systém zvládá v továrně konkrétní díl sledovat napříč celým procesem výroby. Jak to funguje?
Můžeme mít výrobní stanoviště rozmístěná po celé výrobě. Typicky se to používá tehdy, když máte výrobek, ke kterému postupně přidáváte komponenty a potřebujete zkontrolovat kvalitu před tím, než se produkt zakrytuje. K tomu stačí mít po lince rozmístěné kamery, případně jiná zařízení a jen průběžně kontrolujete stav výrobku. Naše vize je ale sledovat cestu výrobku napříč továrnami. Chtěli bychom udělat tzv. protokol kvality, který je schopen sdílet informace skrz jednotlivé závody. V automotive máte na konci řetězu OEM (Original Equipment Manufacturer, výrobce koncového zařízení Škoda, Hyundai atd.), což je linka, která z předpřipravených komponent skládá finální auto. Pod OEM jsou ale různé výrobní závody, které vyrábějí dílčí produkty nebo komponenty. Továrny si postupně předávají komponenty, ke kterým na každém stupni každá něco přidá, až vzniknou hotové výrobky, které OEM smontuje k sobě.
A ideálem je sběr dat ze všech úrovní procesu?
Ano, aby následný nebo koncový dodavatel věděl, jaká je kvalita dílů v celém cyklu. To je asi největší přání výrobců, protože tam existuje velký tlak na kontrolu kvality. Pokud kvalita ale není dokazována a dokumentována, tak výrobci zpřísňují pravidla, a to někdy až zbytečně moc. Výrobce pak zbytečně zahazuje desítky procent vadných kusů jen z obavy, aby nedostal pokutu. Přitom odběratel by je možná i přijal. Kdyby ale celý proces byl dostupný v reálném čase, tak jednotlivé stupně by mohly průběžně kontrolovat závažnost vad a zefektivnila by se celá výroba.
Systémy v moderních továrnách, navíc těch automatizovaných, bývají značně složité. Jak těžké je v takové situaci integrovat to vaše řešení do už zaběhnutých systémů?
Určitě to není nic lehkého. Postupně budujeme různé případové studie a scénáře. Začali jsme od těch nejsložitějších případů, protože kromě asi 30 menších pilotů máme i velké výrobce – Škodovku a Hyundai. V obou případech potřebujeme komunikovat s jejich systémy. Náš systém je postaven jako moderní cloud native aplikace s API rozhraním. V API rozhraní máme nastavené parametry, které potřebujeme posbírat, a jsme flexibilní v integraci výstupů k zákazníkovi. To znamená, že přizpůsobíme kód jen podle konkrétní aplikace, CRM nebo MESu a pak už získáváme data od zákazníka. Technologicky to není problém téměř vůbec. Procesně to ale už problém je, protože většinou, abyste se dostal do katalogů výrobků Škodovky, který se mění téměř každý den, tak vás poměrně dost dlouho zdrží různá schvalování přístupů apod. To může zabrat i pár měsíců. S tím musíme počítat a i při pilotních projektech většinou začínáme tím, že pilot je ze začátku bez přímé integrace, a až když se ověří funkčnost a kvalita, pak přistupujeme k integraci.
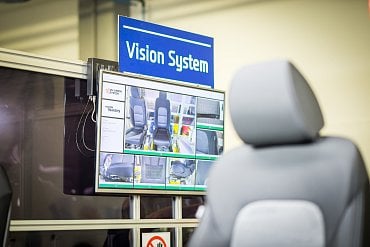
Uplatnění 24 Vision Systems podle Cvička nahrává hlavně to, že platforma zvládá odvádět dobrou práci i při vysokém tempu produkce.
Vím, že se to dá velmi těžko zobecnit, ale dá se vyčíslit, kolik práce a peněz váš systém zvládne ušetřit?
Propočet efektivity vždy děláme před tím, než dodáváme řešení zákazníkovi. Liší se to případ od případu. Životní cyklus řešení máme rozdělený na 3 úrovně, první je rapid prototyping, potom pilot a nakonec reálné nasazení v produkci. Rapid prototyping vypadá tak, že zajdeme k zákazníkovi, den dva tam fotíme, analyzujeme proces a řekneme, jestli je reálné náš systém nasadit, nebo ne. Případně dostaneme od zákazníka 100 kusů vadných výrobků a v laboratoři uděláme analýzu. A součástí této fáze je i propočítání ROI (Return Of Investment), to znamená, že spočítáme, kdy se systém zaplatí. Nikdy nejdeme do projektu, který by se nezaplatil do dvou let, protože potom to ani pro zákazníka není až takový přínos. Jsou ale i případy, kdy má zákazník ROI počítaný na půl roku.
Pojďme si teď popovídat přímo o vaší firmě. Kolik má 24 Vision Systems zaměstnanců?
V mateřské firmě TinT z Frýdku-Místku je 50 lidí, přičemž ve 24 Vision Systems, který je už rok samostatnou firmou, pracuje 12 lidí. Převážná část dělá na vývoji a rozvoji produktu. V příštím roce budeme určitě nabírat, ale žádné stovky lidí, spíš v rámci desítek procent. Do konce roku by nás mělo být asi 20.
Jak se na růstu firmy projevil letošní rok? Kvůli koronaviru se totiž automotive dostalo obecně do problémů.
Pandemie se určitě negativně projevila v tom, že jsme nemohli osobně jednat se zákazníky, což je pro nás v této fázi klíčové. Všechno se řešilo přes Skype nebo telefon. Negativní dopad byl rozhodně v sales a marketingu. Měli jsme mít letos asi tři výstavy, z toho jednu v USA, dvě v Německu, měli jsme na ně i domluvenou dotaci od CzechInvestu. To vše padlo. Na druhou stranu technologicky a byznysově nám to spíš přihrává, protože automatizace pomáhá snížit závislost na přítomnosti lidí ve výrobě, částečně je totiž nahrazujete stroji. Na to dnes firmy čím dál víc slyší. I přesto, že jsou třeba ve fázi úspor, tak tyto projekty nechávají otevřené a snaží se automatizovat, kde to jde.
Uspěli jste také v soutěži CzechInvest Startup Challenge. Pomohlo vám to už nějak konkrétně?
Určitě to má marketingový dopad, protože se o tom hodně píše. Zákazníci nám třeba posílají články o našem úspěchu. A tím u klientů určitě vzbuzujeme důvěru. Obchod totiž vždycky děláme osobně. I když příští rok plánujeme expandovat do Německa a Španělska, tak počítáme s tím, že veškerý obchod budeme dělat osobně. Zákazník ale potřebuje mít důvěru podpořenou i nějakým externím zdrojem a tohle jsou přesně ty akce, které nám pomáhají tu důvěru u zákazníků získat.
Takže letos se vám navzdory komplikované situaci dařilo. Jak se to promítlo do hospodářských výsledků?
Na konci loňského roku jsme byli v akcelerátoru StartupYard, od března do června jsme dost aktivně jednali s několika investory a přes prázdniny jsme s jedním investorem podepsali seed investici. Tu budeme čerpat do konce příštího roku. Na nule se snažíme být alespoň v rámci sales. Letos jsme měli obrat v řádech několika milionů. Dalším dopadem letošní situace je, že zákazníci jsou více opatrní a snaží se přejít z investičních nákladů na operativní náklady. Nasazení kontroly kvality je investice v řádu milionů korun a kvůli tomu, že výrobci dnes spoří, vítají spíš pilotní case, kdy si účtujeme jen subscription poplatek a necháme pilot běžet čtvrt roku. A instalace do provozu se domlouvá až následně. Z tohoto pohledu jsou naše příjmy trochu posunuté a obecně je životní cyklus každého projektu v řádu měsíců. I když teď máme rozjetých nějakých 30 pilotních studií najednou, tak očekáváme, že reálný výsledek přinesou až v druhé polovině příštího roku.
Zmínil jste, že máte investora. O koho přesně jde?
Je to investiční skupina M.L. Moran a konkrétně pan Šmejkal (Zdeněk Šmejkal, spolumajitel skupiny, pozn. red.). Měli jsme tři nabídky, z toho dvě byly klasické venture capital fondy, třetí byla tato a dlouho jsme nad tím přemýšleli. Pan Šmejkal má za sebou hodně úspěšných projektů, a teď se navíc ponořil do Industry 4.0. Chtěl by vybudovat fabriku „na klíč“, a když to začal dělat, chyběla mu oblast kvality. Na trhu nenašel nikoho, kdo by byl schopen tuto oblast pokrýt. Pár měsíců jsme si o tom povídali a vzešla synergie, takže jsme si nakonec plácli. Není to tedy čisté venture capital spojení, ale spíš joint venture, kdy my se můžeme zaměřit na vývoj technologií a pan Šmejkal nám pomáhá v obchodu, strategii a sales.
A co plánujete do příštího roku?
Určitě vstup na německý trh. Už dnes, díky tomu, že máme zajímavé zákazníky, kteří mají buď centrálu v Německu, nebo jako Škodovka mají v Německu svou mateřskou firmu, tam přes tyto společnosti pronikáme. A co se týče technologických věcí, tak kromě rozšiřování produktu ho určitě chceme daleko více integrovat s automatizací, kolaborativními roboty a mít takové autonomní řešení kvality.
Když už zmiňujete Německo, hodně se mluví o továrně Tesly, která vyroste u Berlína. Tesla je proslavená až přehnaným důrazem na automatizaci. Nabídnete vaši technologii Elonovi Muskovi?
Stoprocentně to máme v plánu, dokonce jsme na Teslu měli i nějaký kanál přes spolupracující univerzity. Uvidíme, třeba se to podaří. Elon Musk je pro mě vzor, takže to by bylo super.